Improving Production Workflows in Industrial Facilities
In the challenging environment, improving production flows in manufacturing facilities is crucial for upholding efficiency and boosting profitability. With progress in technology, industries are turning to new cutting solutions such as precision and water jet cutting services to streamline processes and improve product quality. These methods not only provide precise cuts but also greatly reduce waste and downtime, allowing manufacturers to meet increasing demands without sacrificing on standards.
As producers strive to achieve operational excellence, understanding the unique benefits and applications of various cutting techniques becomes important. Laser cutting offers high-speed precision, making it perfect for detailed designs and fragile materials, while waterjet cutting is celebrated for its flexibility and ability to handle heavy materials without heat distortion. By incorporating these cutting technologies into their production flows, facilities can enhance efficiency, cut costs, and improve overall output, setting the stage for sustainable growth in an ever-evolving market.
Overview to Laser & Waterjet Cutting
Waterjet and laser cutting services have revolutionized the manufacturing industry by delivering highly efficient and precise methods for cutting materials. Laser cutting utilizes focused light beams to melt, burn, or vaporize materials, which allows for exceptionally intricate designs and tight tolerances. It can be used on a diverse array of substrates including wood, metals, and plastics, making it a adaptable choice for various manufacturing applications.
Waterjet cutting, makes use of a high-pressure jet of water mixed with abrasive particles to cut through materials. This method is particularly suitable for more substantial materials or those that are sensitive to high temperatures, as it does not cause thermal distortion. Waterjet cutting can work with an variety of materials, including ceramics, glass, and composites, making it a crucial tool for industries that require varied manufacturing abilities.
Both laser and waterjet cutting techniques not only boost the quality of production but also enhance overall workflow in manufacturing facilities. By utilizing these cutting services, manufacturers can increase their throughput, reduce waste, and refine the accuracy of their products, ultimately leading to greater efficiency and competitiveness in the market.
Benefits of Optimizing Production Flows
Improving production flows in factories brings about considerable improvements in efficiency as well as performance. By simplifying processes, businesses are able to reduce time and resource consumption required for finishing tasks. This not only improves production output but also minimizes losses, which enables businesses to focus on maximizing ROI. A streamlined production flow can markedly cut turnaround times, enabling quicker responses for customer demands and market changes.
Additionally, this optimized flow can boost final products. If production operations are designed for seamless transitions and fewer interruptions, the chances of mistakes as well as problems diminishes. Such precision is extremely important in industrial cutting applications, such as laser-based as well as water jet cutting, where accuracy is critical. Improved flow results in a more consistent and product quality, promoting higher customer satisfaction as well as returning customers.
Moreover, enhancing production flows can contribute to staff morale as well as employee safety. A properly organized operation enables employees to concentrate on their job duties without the stress of navigating through disorganized processes. Streamlined facilities minimize the likelihood of incidents, since hazards linked to cluttered as well as disorderly environments are minimized. This improved work environment not just boosts performance and also aids in keeping skilled employees, resulting in a more stable as well as qualified personnel.
Case Studies and Effective Strategies
In recent years, a premier aerospace manufacturer adopted a dual approach using both laser and waterjet cutting service s to improve its production efficiency. The facility integrated laser cutting for thinner materials, which provided superior accuracy and speed, while waterjet cutting was employed for heavier, more resilient materials that required a distinct treatment. This tactical combination allowed the manufacturer to enhance its workflow significantly, cutting down on production time and waste while maintaining high quality standards.
Another pertinent example can be seen in the automotive industry, where a company adopted waterjet cutting for intricate components needed for its vehicles. By capitalizing on this technology, they were able to minimize the thermal stress that often comes with traditional cutting methods, thereby maintaining the integrity of the materials. Furthermore, this adaptation resulted in fewer tool changes and a smoother production line, ultimately leading to enhanced output and lowered costs.
Lastly, a small-scale fabrication shop demonstrated the benefits of investing in both technologies by offering customized services to a varied client base. By positioning themselves as a one-stop solution for both laser and waterjet cutting, they boosted their customer reach and satisfaction. This flexibility not only helped the shop stay competitive in a crowded market, but it also encouraged innovation, as they could tackle unique projects more efficiently with the right tools at their disposal.
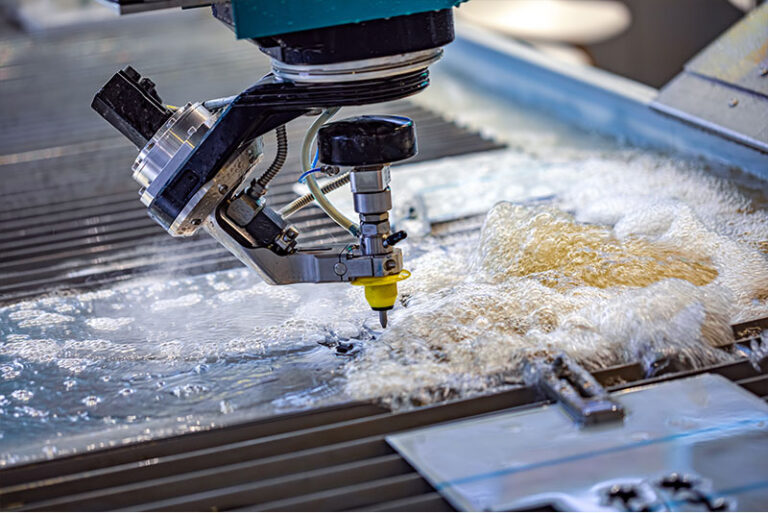